
| WASTE EN RECOVERY SYSTEM | INK WASTE RECYCLING SYSTEM | WASTE WATER REUSE SYSTEM | KMnO4 RECYCLING TECHNOLOGY | HCl RECYCLING TECHNOLOGY | SOLAR ENERGY REGENERATION SYSTEM |
KMnO4 RECYCLING TECHNOLOGY |
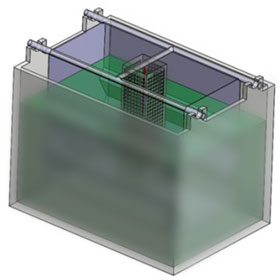 |
In the electroplating process, the oxidation of the substrate material is not conducive to the plating, before we deal with the substrate material to the substrate material pre-processing. This process is called bright dipping for steel materials, will immerse the metal in a solution of KMnO4. However, the chemical reaction of the removing of the surface oxide consume a lot of KMnO4. Epson has developed a KMnO4 regeneration system, through recycling, reprocessing, so that companies can greatly reduce the cost of processing.
Specifications (Can be Customised to Customer Requirements) |
Size: |
500 (L) × 300 (W) × 500 (H) |
Treatment Volume: |
800L and more |
Concentration Range before treated: |
KMnO4 : 15g/l, K2MnO4 : 50 g/l and more |
Concentration Range after treated: |
KMnO4 : 45g/l , K2MnO4 : 20 g/l and more (300% Regeneration), |
Treatment Time: |
6 hours or more depend on treatment volume |
Capacity: |
KMnO4 : 24kg per treatment or more (Subjected to treatment vol) |
Advantage |
Per hour Processing of 3g / l
|
Reduced 50% of Industrial Water
|
Very Small Covering Rate
|
Easy Installation Operates Safely
|
Reduces Cost
|
Back To Top
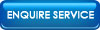
|